Por:
Néstor Chávez-Duarte, Asistente de Extensión I de Cenipalma
Durante el año 2022 se presentaron los resultados del seguimiento a los costos variables de procesamiento de racimos de fruta fresca (RFF). Este estudio contempló la participación de 20 plantas de beneficio a nivel país. Se utilizó una metodología de recolección y análisis de la información generada y aprobada por los Comités Asesores de Plantas de Beneficio. Entre los resultados del estudio, se obtuvo un costo promedio de procesamiento por tonelada de racimo estimado en 57.267 COP con una distribución del costo total en los siguientes rubros: mano de obra 40%, mantenimiento 38%, servicios industriales 19%, gestión ambiental 1% y otros costos 2%. (Guerrero, Mosquera & Cala, 2023, p. 3)
Como una actividad complementaria al resultado del seguimiento de costos nacional, se realizó un ejercicio de análisis de los aspectos asociados al comportamiento del costo de los servicios industriales; eficiencia, costo de la energía y cogeneración, para los datos recolectados en nueve plantas de beneficio de la zona central del país.
El 19% del costo total de procesamiento por tonelada de racimo de fruto fresco, corresponde a los servicios industriales. Estos servicios se clasifican en dos categorías principales: el consumo de energía y el consumo de agua. El consumo de energía representa el 92,2% del costo de los servicios industriales, e incluye la energía proveniente de la red pública, la generación a partir de combustibles fósiles y la cogeneración. El consumo de agua representa el 7,3% del costo de los servicios industriales, y tiene un papel fundamental como fuente de energía térmica en el proceso de producción, además de su uso en fines domésticos e industriales.
- Lea también: Hidrógeno verde y transición energética: ¿una oportunidad para el sector palmero colombiano?
El análisis para Zona Central mostró variabilidad en el costo de los servicios industriales entre las plantas de beneficio, oscilando entre $6.080 / t RFF hasta $14.700 / t RFF. Este costo depende de cuatro factores principales:
- La eficiencia de consumo de energía
- El costo por kilovatio de energía de red
- El costo y la proporción de uso de combustibles fósiles en la generación auxiliar
- La participación de la energía autogenerada en las plantas que cuentan con estos sistemas.
Los datos indican que las plantas de la Zona Central con menor costo en servicios industriales tienen una eficiencia de consumo de energía entre 17,5 y 25 kWh / t RFF, mientras que las plantas con mayor costo tienen una eficiencia entre 28,2 y 41 kWh / t RFF. El costo por kilovatio de energía de red, que varió entre $321 / kWh y $521 / kWh en la Zona Central, depende de múltiples factores, como el tipo de generación, la demanda de cada planta, el tipo de tarifa, el tipo de tensión, el costo unitario (CU), los cargos por uso, confiabilidad y contribución, etc.
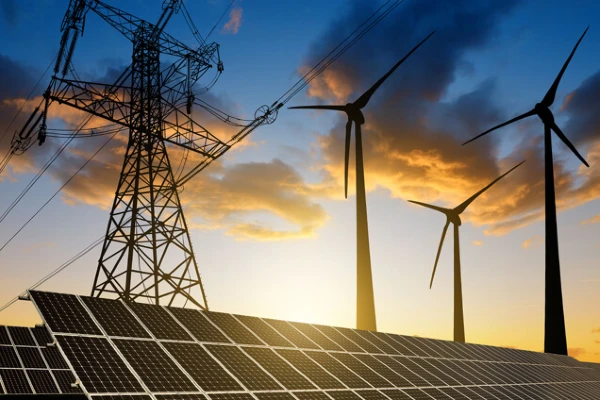
En cuanto al uso de combustibles fósiles para la generación auxiliar, el costo de generar 1 kWh mediante diésel osciló entre $329 / kWh y $1.505 / kWh. Este costo se ve afectado principalmente por la disponibilidad y el transporte del combustible, que están sujetos a la ubicación geográfica de las plantas y en ocasiones a problemas de orden público. También influye la eficiencia de los generadores auxiliares en la producción de energía y el porcentaje de uso de energía diésel en el total consumido del año.
La cogeneración de energía es una práctica que reduce el impacto del costo de la energía total, sobre todo en zonas donde el acceso a la energía de red es más costoso. El costo promedio por kWh de energía cogenerada fue de $159 / kWh, según los datos del estudio. Sin embargo, el uso de sistemas de cogeneración no garantiza los costos más bajos en los servicios industriales, sino que se debe combinar esta práctica con una planta eficiente en el consumo de energía por tonelada de RFF, disminuir la utilización de generadores diésel y aumentar el factor de utilización de la energía cogenerada por encima del 80% en relación con el total consumido, para obtener resultados satisfactorios en el costo final.
Por último, el costo del uso del agua en el proceso industrial, principalmente usada para generación de vapor, varió entre $207 / t RFF y $950 / t RFF para plantas sin cogeneración y en promedio $1.240 /Ton RFF para plantas con cogeneración. El costo del agua también depende de la fuente, el tratamiento y el volumen utilizados.
Mejores prácticas relacionadas con el consumo de energía en plantas de beneficio
- Implementar planes de ahorro y uso eficiente de la energía, que incluyan la identificación de equipos de alto consumo, la reducción de pérdidas de energía y la evaluación de equipos sobredimensionados, así como la optimización de la tensión. Estas medidas pueden mejorar la eficiencia en el consumo de energía en el complejo industrial, lo que a su vez reduce los costos totales.
- Realizar un análisis estratégico en la ubicación de las instalaciones industriales, que tenga en cuenta los factores que influyen en el costo de la energía. Para reducir este costo, se pueden considerar opciones como acuerdos o subsidios de energía con el proveedor de servicios, la adopción de fuentes de energía alternativas, selección de horarios de consumo privilegiados o la elección de la tensión eléctrica adecuada.
- En el caso del uso de energía cogenerada, maximizar su utilización, ya que el costo final está directamente relacionado con el grado de participación de esta fuente de energía en el total consumido en el proceso industrial. Estas fuentes son una ventaja para plantas con difícil acceso a la energía pública, redes inestables que no permiten la continuidad del proceso y plantas que contemplan altos consumos diferentes a los netos del proceso.